Terminal crimping is an important process in wire harness processing, but many customers report that defective products will be produced during the operation. How to reduce crimping defective products and improve the efficiency and quality of wire harness processing?
The editor today compiled a practical dry goods for everyone, and analyzed them from two aspects: pull force and terminal cross-section analysis.
Pull force
The pulling force NG is generally related to the plasticity of the wire and the crimping force. Today we will mainly explain from the crimping force. In the wire harness drawing process, the core wire part bears the greatest tensile stress, and the middle layer has the smallest surface.
Common situation of pulling force NG
1. Too much pressure causes internal cracks in the copper wire of the wire.
2. The pressure is too small, and the connection between the terminal and the wire is not firm.
Improve methods
If you find that the terminal pressure is too tight, you can increase the crimping height appropriately.
If the pressure is too loose, the crimp height can be appropriately lowered.
(PS:Due to different wires, you can refer to the crimping height range of different wires below to adjust in actual operation£©
Terminal section analysis
Terminal cross-section analysis is a more accurate and comprehensive method to detect the quality of crimping force. Through cross-sectional analysis, you can clearly and intuitively understand where the problem is, and then make adjustments and improvements.
The standard terminal riveting section section is shown in the figure¡ý¡ý¡ý
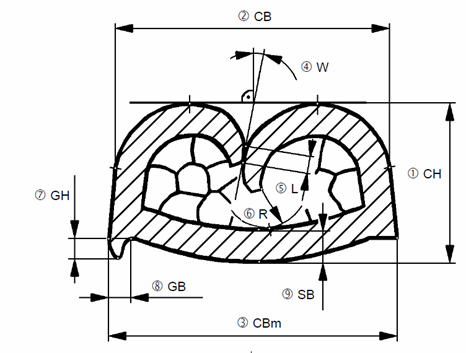
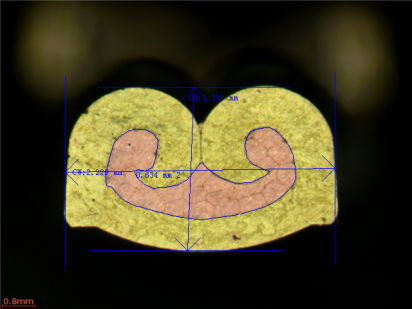
Common situation of terminal section NG
l The core wire is loose and the conductor has no obvious deformation
l The crimping wings are not completely closed
l The crimping wing touches the package tube or is asymmetrical
l There is a vacancy in the terminal
l The burr is too high or too wide cracks in the terminals
Improve methods
The core wire is loose and the conductor has no obvious deformation.
The core wire of Figure 1 is loose and there are gaps, and the conductor of Figure 2 has no obvious deformation, all of which are related to the compression ratio. Just increase the pressure.
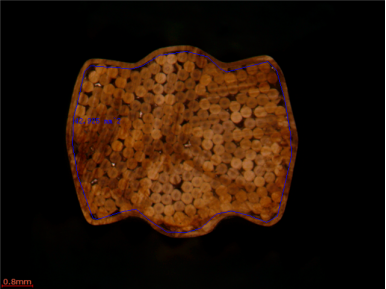
The crimping wings are not completely closed.
Generally divided into the following two situations: 1. The core is too large. Use a core with a smaller OD. 2. The crimping die is not suitable. Use terminals with larger crimping area.
The crimping wing touches the package tube or is asymmetrical.
The crimping wing touches the bottom or side of the package barrel because the crimping height is too low, and the crimping height needs to be adjusted. 2. The crimping wing is asymmetrical, so you need to adjust the upper and lower die until it is symmetrical.
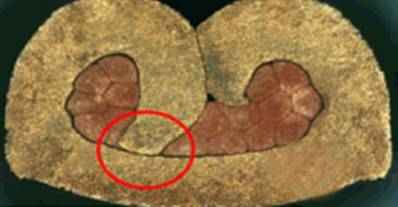
There is a vacancy in the terminal.
When the wire core has been compressed, there is a vacancy in the terminal. Generally, the wire does not match the terminal die, and the die needs to be replaced.

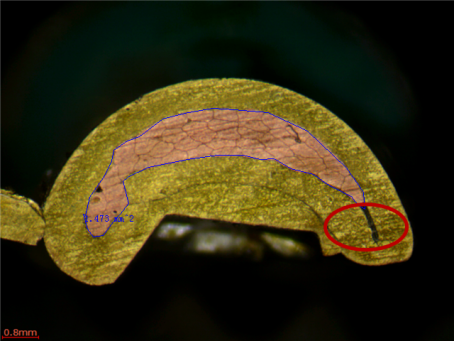
The burr is too high or too wide.
The normal range of burrs: height <0.1mm, width <0.5mm.
Figure 1. The width of the burr obviously exceeds the requirement. This phenomenon is generally caused by the wear of the crimping bottom knife (base), and the crimping bottom knife needs to be checked and replaced.
Figure 2, the height of the burr obviously exceeds the requirement. This phenomenon is generally related to the height of the crimping die. The crimping height needs to be adjusted. It may also be caused by the misalignment of the upper knife and the lower knife, and the crimping die needs to be adjusted.
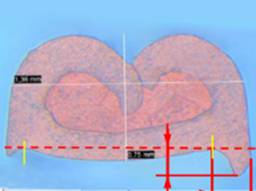
Cracks in the terminals
There are obvious cracks on the inner wall of the package cylinder, which means that the slicing position is close to the serrated groove. Continue to grind the cut surface. Normally, the crack will disappear. If the crack does not disappear, mainly check the terminal material, and then adjust the crimping die¡£
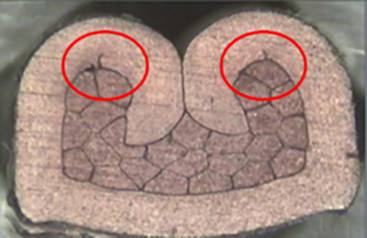
----Your reliable wire harnessing equipment solution supplier --- Eastontech